Hygienic Cables that Power the Food and Beverage Industry
-
LAPP Tannehill
- Wire & Cable
- Nov 10, 2023
- 3250views
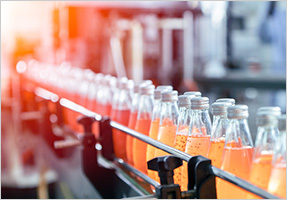
Hygienic Cables that Power the Food and Beverage Industry
Written By: Denisse Miranda, Marketing Automation Manager at LAPP
Let's explore why food and beverage manufacturers should prioritize quality and food safety to reduce downtime when selecting hygienic cable solutions.
Let’s review what manufacturers need to prioritize in order to offer the right cable solutions to end users in the food and beverage industry. Then, we’ll look at what LAPP Tannehill has to offer.
High-Quality & Sustainable Products
In today’s evolving food and beverage industry trends, consumers tend to look for healthier options, supply chain transparency, and high-quality and sustainable products.
>> Learn how LAPP plans on continuing sustainability efforts in the foreseeable future.
Due to this demand for higher standards in the industry, it is important to choose the right cable solutions for your manufacturing facility. The more reliable your cables are, the better you can meet consumer expectations and yield returning customers.
Product consistency is a cornerstone of success in the food and beverage industry. Uninterrupted cable performance is vital for keeping machinery and equipment in continuous operation.
Reliable cables help ensure that products are consistently of high quality and that there are no disruptions in the production process.
By using dependable wire and cable solutions, companies can minimize downtime due to cable failures and maintenance issues, leading to increased productivity and cost savings.
Downtime in the food and beverage industry can be costly, not only in terms of lost production but also in potential product wastage. In an industry where time is money, minimizing disruptions is critical.
Food Safety Regulations
Food safety regulations are not to be taken lightly. The consequences of non-compliance can be severe, including product recalls and legal repercussions.
Using hygienic cables that adhere to food safety standards ensures that manufacturers meet these strict regulations and maintain the highest level of food safety. This is especially important when in your manufacturing process your cable or equipment enter in direct contact with meat, poultry, fish or similar.Â
The Food Safety Modernization Act (FSMA), which was signed by presidential order in 2011, states that food producers must take all necessary steps to prevent foodborne illnesses and pathogens.
In the past, machine operators waited until E. coli or other bacteria had already grown before taking any measures—they solved the problems after they occurred, instead of taking measures to prevent them.
Some materials, such as stainless steel, can handle harsh cleaning regimens for the long haul. But some plastics cannot. Using plastics or elastomers when they are not suitable for frequent cleaning can make system parts lose their protection rating and cables can lose their insulation properties.
Read more about maintaining cable hygiene: Clean Cables and Connectors for Food and Beverage Machines
To meet stringent hygiene standards, it is necessary to assess each component of a food and beverage production system for its susceptibility to promote the proliferation of microorganisms. This assessment includes the examination of cables and associated electrical elements.
Bacteria and other microorganisms can actively consume the polymeric components of cables, leading to both contamination and deterioration of the cable's insulation.
The expensive consequences of cable malfunction include reduced production output, failure to meet sanitation requirements, or prolonged periods of inactivity.Â
LAPP Tannehill offers various cables and components that resist microbial growth and reduces the risk of failure.
ÖLFLEX® FD Flexible Robotics Cables
The ÖLFLEX® FD cable range stands out as one of the most flexible cable options available, with several options that are suitable for the Food & Beverage industry processes, and especially for those seeking to take the next step in technology and automation in their process.Â
These cables are specifically engineered for advanced technological applications, particularly in environments where automation has reached an elevated level, and where traditional cables may experience fatigue due to the stresses placed upon them.
In situations where automated handling equipment and robotics are in continuous operation, the enhanced flexibility of this range can endure more demanding and heavy-duty tasks.
Throughout the cable's construction, careful attention has been devoted to areas that are vulnerable to stress.
This includes using finely stranded wire conductors with a high degree of twisting among the strands and within the conductors forming the core bundle.
The increased twist rate serves to reduce stress on the conductors when subjected to bending.
Additional features of this cable range encompass added chalk, textile separator tapes, and a specially formulated Polyurethane sheath that resists hydrolysis and microbial growth.
- ÖLFLEX® FD 855 P: power & control cable with small bend radius for restricted areas and Polyurethane sheath
- ÖLFLEX® FD 855 CP: power & control cable with small bend radius for restricted areas, copper braid screen, and Polyurethane sheath
- ÖLFLEX® FD VFD: shielded, continuous flex motor supply cable with a minimum bend radius
SKINTOP® Hygienic Cable Glands
What if the cable is right, but you still have problems? Using the incorrect cord grips/cable glands might degrade your cables faster, causing downtime.
LAPP has created SKINTOP®, a line of specialized hygienic cable gland, manufactured from high-grade stainless steel, suitable for a wide variety of applications while also adhering to strict conditions from food and pharmaceutical industries.
The following products are stainless steel cable glands with smooth surfaces designed for use under tough conditions and therefore have a high chemical and mechanical resistance:
The following products are corrosion-resistant stainless steel cable glands with smooth surfaces, a compact design, and are sea water-resistant.
Examples of Applications for Food & Beverage Cables
- Dairy processing/technology
- Meat and fish processing
- Baking and confectionery processing
- Bottling plants
- Packaging machines
Read these articles and case studies on how these manufacturers used the right hygienic cable solutions for their use cases:
- LAPP Cables Power Cheese-Making Machines
- Using SKINTOP HYGIENIC Cord Grips with Ultrasonic Sensors
- Flexible Tray Cable & Hygienic Cord Grips for Breweries
Do you still have questions regarding your hygienic cable for food and beverage applications? Chat with us!